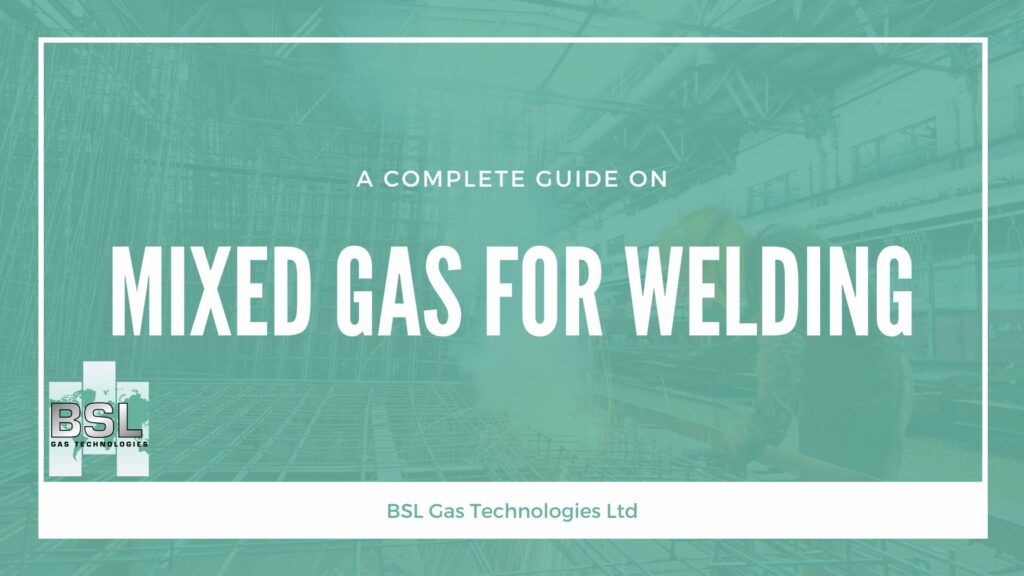
With industry products ranging from cosy pubs to manufacturing giants, a huge application of our technology lies in the precision supply of mixed gases to welding stations, both manual and robotic .
Welding is a fundamental process; it unites metal components through the gentle heating of a targeted area and a compatible filler metal until the edges meld together. This technique allows for the creation of intricate shapes without the exorbitant costs associated with casting or machining.
As heat transforms metal, a mixture of gases above the weld pool are introduced to act as a safeguard against unwanted air exposure.
Air itself is a mixed gas. An amalgamation of nitrogen, oxygen and water vapour, it poses challenges when introduced to a joint during welding. Under heat, nitrogen forms tiny, solid beads within the weld, leading to brittle joints and cracks. Similarly, oxygen’s interaction with metals such as iron can result in rust, jeopardising the structural integrity of the weld, and water vapour contains hydrogen which can lead to issues like porosity and hydrogen embrittlement.
This handful of problems is what led us on a search for something better than air as a shielding gas, and we had a list of requirements to go along with it:
The chosen gas needed to be chemically inert, thwarting the risk of brittle joints. Alongside this, its weight had to surpass that of air in order to withstand drafts during welding. Cost-effectiveness was paramount, and argon emerged as the go-to base gas. Comprising a mere 0.9% of air’s composition, argon formed the bedrock for an optimal gas blend and it was from here that the controlled additions of other gases could begin.
Carbon dioxide is the single most common additive in the production of shield gases. It enhances weld penetration and its composition can be tailored to the material’s thickness. In Europe and the East, most common applications require concentrations around 20%, while the American norm reaches 25%.
The strategic inclusion of oxygen in modest proportions (2-5%) within argon-based mixes has been shown to improve arc stability and reduce molten metal tension during welding. ‘Crude’ argon’s natural oxygen content of around 2% streamlines the creation of branded mixes by combining carbon dioxide and crude argon in precise measurements.
This is where the beauty of a BSL system shines through. If a customer makes the decision to shift away from a specific branded mix, a common worry may be that they will no longer have access to the precise mix of gases they had before. Using our three gas mixers, we are able to precisely replicate any desired mix, ensuring continuity in welding operations.
Hydrogen in any amount is bad news for most steels, aluminium or magnesium. But like oxygen, it can be beneficial for use in applications such as nickel, copper and some stainless steels. By narrowing the arc and increasing the arc temperature, hydrogen can enhance weld penetration.
The rule of thumb when sizing gas mixers for welding.
The ideal approach for sizing a welding application is to consider the number of welders and their corresponding mixed gas flow rates. If this information isn’t readily available, a recommended starting point is a flow rate of 16 l/min (at 1.013 bar and 293K) per welder. This translates to roughly 1 m³ /hr. Once the number of welders has been established, we are able to offer the customer a mixing panel in the most appropriate size for their application. Because it is unlikely that all welders will be operating simultaneously, there is always likely to be enough capacity for leaks!
Manufacturing processes often demand larger volumes of mixed gases, leading to the use of liquid supplies delivered in bulk. While one gas may be supplied in bulk, smaller quantities of another, which constitute a smaller portion of the final mix, may be delivered in a multi-cylinder pack. Irrespective of the delivery method, a Gas Mixer is employed to precisely create the required final gas blend for the customer’s specific needs.
Our focus is on reducing electrical components wherever feasible and eliminating the necessity for buffer tanks post-Gas Mixer.
By reducing the need for electronics and buffer tanks, our systems become simple and readily operational upon delivery. Alongside this, every piece of gas mixing equipment that leaves our headquarters comes pre-certified for its required calibration settings.
Combined, these two elements are steadfast to reduce maintenance costs due to the absence of solenoid valves that could deteriorate over time. Our pre-set gas mixers meet most customer demands, while adjustable versions are also offered. Our standard modules serve applications up to 250 and 300 nm³/hr, with our range extending to systems up to 1000 nm³/hr.
By eliminating the requirement for electronics and buffer tanks, our systems become uncomplicated and instantly operational upon arrival. Additionally, each piece of gas mixing equipment that departs from our main facility is already certified for its necessary calibration settings.
These two factors combined work effectively to cut down maintenance expenses by removing solenoid valves, which can degrade over time.
We are your one-stop-shop for all your gas mixer manufacturing and engineering needs. Our team of experts can deliver customised solutions tailored to your specific requirements. If you can’t find what you’re looking for on our website, don’t worry, we have got you covered.
If you’re interested in reading our other blog posts, you can do that here. Make sure you’re following us on LinkedIn, Facebook, Twitter and YouTube so that you never miss an update from us.